I start this article with listening, as that truly comes first. Learning and leading follow. Used together, these tools can make the construction site a much safer place indeed.
Listening
When I was on the farm, we broke the axle on a piece of equipment that cut grass to bale. Dad took me to the John Deere dealer, and the conversation went like this: "Max, my haybine is in the middle of the field on its belly. Broke most of the knives, so I need a dozen or two, and the main axle sheared right off." "Well, Robert, I never had an axle break on a haybine since I owned this place. But, let me get you one." (As an aside, dealer Max was no fan of my dad.) As Max left to grab the part, Dad whispered to me, "If they never break, why does he keep them in stock?" This was my early lesson on listening.
In construction, we easily criticize the guy falling off a ladder. "Of course he fell, he was on the top step!" If we had asked the injured worker and listened to why he was on top, he likely would have replied, "That's the ladder they gave me."
My firm works in semiconductor factories and manufacturing plants across the U.S. Today, we celebrated one full year without a recordable incident at our largest site. Most of our projects are routinely injury-free. At a recent site gathering of safety managers from other trades (and our client), the conversation centered on how some of the workers could just not "get it," and the thought was offered that stricter requirements or more scrutiny would turn them around. We offered that we had a similar project 20 miles away that many considered a safe, model site. No injuries, no drama and a happy workforce.
We proposed a challenge to the group. (This is the "leading" part of our safety philosophy and why our firm is considered a leader in our field.) We told them (not suggested) that we would interview that model project's team and share what was working at their site with everyone.
So we took the time to listen to our "model" team: John Wood and Steven Enright, our safety managers; Mario Gabriel, our project director; and Brian LaRosa, one of its foremen, who truly stands out. These guys were excited and happy that someone took the time to listen. Filming was simple: a cellphone on a stand in a break room and lighting supplied by a window. It was a big success, and the lamenting group, after watching our interviews, went on and interviewed 30 other folks in the field who know what works. That's how you lead. You may think it odd I included the names of our team, but we need to recognize success more often and spend less time publishing rates that highlight our misfortune.
See also: Adopting New Standards of Safety
Summing up, take the time to listen to those doing the work. When there is an accident (remember the guy on the ladder?), interviews are the first thing we do to learn more about what went wrong. Consider the power of asking what he needed to be safe—before he fell. And then remember to thank the person who taught you. It is critical to let those who share their tips know how valuable they were to others. Before you move on to your next battle, thank the warriors from the last.
Learning
I love the idea of simplification. I do not like clutter. So when I spotted the practice of piling as many tools on a cart as we can to take into a clean room, I asked why? "Well, that's how we have always done it." That, of course, grabbed my attention. But, consider the fact that a pilot uses the same preflight checklist every time. If you ask him or her why, the reply may be: "We have always done it this way." Considering we have not had an air disaster in the U.S. in years, we do need to listen and learn from the experts. However, remember, someone once suggested the idea of a checklist to a pilot.
So, I reviewed the data for the last few years—had we ever had an incident or injury from a messy cart? No. Does the cluttered cart pose a hazard to anyone? Kinda. Have we ever had complaints from the customer on how we use and store these carts? Yes. Should we take the time to organize these carts to simplify? Yes—but with the users. To step in and organize a good worker's cart or toolbox would be like rooting around in my wife's pocketbook; something you never do. New to safety, I was once pointedly told by an upset ironworker in Philadelphia (as I searched through his gang box for unsafe things) that you need to ask the owner first and then look with him, my listening lesson.
Back to learning and listening. When I asked a foreman why the cart was often messy, he replied that it was a real hassle to leave the work area (clean room), ungown, get the tool he needs, wipe down the tools, regown and return to the work area. That system was the contributor to clutter. I asked why he didn't install a simple shadow box rack on top to hang his tools; his answer: "They just give me the cart.…" I replied, "If we can cut down the time it takes for you to search through the clutter to find your level and make sure everything you could possibly need is on the cart, would that make the job easier and faster?" That's what we are figuring out, together, today.
Great workers treasure their tools and are proud of how they are used. Any changes we recommended must answer his or her classic question: "What's in this for me?" The answer we are working toward is for those users to be part of something big (leading) and for them to want to share their knowledge (listening) and then share that outcome with the rest of our company, our clients and the industry (leading).
Leading
Reportedly there is a quote at West Point that goes something like, "Before you can lead, you need to learn to march." Over the course of my career, I have witnessed and worked for firms that are more than happy to just march. The interview approach we just discussed is a great example of stepping up in front of your clients and your competitors to lead. Leading is easier in safety, for we love to share everything we know and do not see another contractor's safety manager as a competitor. We are one of the few groups that strive to protect everyone—not just whom we work for. I call my safety team the "lifesavers" with pride, for that is what true safety professionals are.
The tendency for many firms is to follow because it's easier. But as with a sled dog, unless you are the lead dog, the view ahead is never pretty. I once had the idea of a national database to share lessons learned among general contractors and our owners. The lessons would be filtered through a well-known safety school and made available to everyone. When I proposed the idea to my boss at the time, he told me, "TJ, it's not what you can do for the industry, it's what you can do for this firm." That's following.
Organizations that are content with marching, not leading, will realize little improvement in their safety efforts. Rates will be static, and people will be unhappy. Many of us love to lead, and many of those doing the work with us want to be a part of that. When everyone is involved in leading, you are surrounded by leaders, not followers.
See also: Connected Buildings and Workplace Safety
In one of my most satisfying efforts while working at Turner, I gathered 14 of my safety professionals, and we brainstormed in a basement break room for an hour. While I sat atop a stool wearing a wizard's outfit and cap, we had a focused and fun conversation on what the perfect scissor lift could look like. No suggestion was too wild. What resulted were some of the freshest ideas from some of the best people. We drove that list of suggestions to Canada and met with the largest scissor lift manufacturer in North America. Some of those ideas can now be seen on lifts today. That's leading.
Conclusion
As you plan your day, look for those exciting opportunities to lead, and give others the chance. It will bring a sense of professionalism to you and highlight your company, and, for those doing construction safety work each day, you will see excitement in the ranks and pride in their faces, and everyone will look forward to going to work.
This article was first published on IRMI.com and is reproduced with permission. Copyright 2014, International Risk Management Institute, Inc.
Construction Safety: Listen, Learn and Lead
Used together, these tools -- listening, learning and leading -- can make the construction site a much safer place indeed.
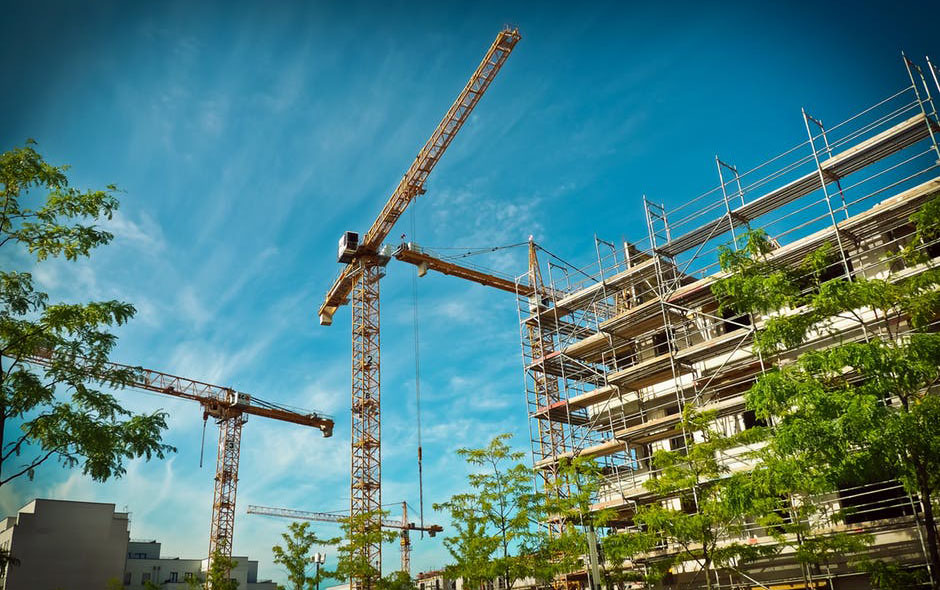