There is absolutely nothing good about a failed water system for the insurer, the customer or the community. One of the most unfortunate things is that many failures are predictable and avoidable -- but not by the plumbers, developers or contractors; the technical assurance of complex systems is the exclusive domain of the engineering discipline. This article demonstrates how a combination of many contributing factors may conspire to compromise an entire system. The insurer should be aware of common pitfalls and mitigate them before accepting the risk. When a failure occurs, the insurer should investigate if the cause of failure has been removed, and where the liability falls. For this investigation, we brought together a hydronic operations engineer, an analytical test engineer and a chemist to reconstruct a more-likely-than-not conclusion for a particular case: a six-year-old CPVC (chlorinated polyvinyl chloride) hydronic system that suffered extensive leaking and catastrophic failures, incurring substantial insurance claims and other economic loads. (A hydronic system uses water to heat and cool a building.) Failure records When leading an investigation, the first thing is to collect the maintenance records, if they exist (an insurer should mandate maintenance plans). These records can then be overlaid on a diagram of the building to see when, where and how severe the problems have been. In this case, there is no clear pattern, which suggests a system-wide failure. Several significant problems were observed during a cursory review of building documentation, installation and operation. There was no single cause of failure; rather, there were multiple conditions. 1. CPVC was not the specified material. In fact, no specifications for hydronic piping material were called out, nor was any statement deferring the material selection to another party apparent. 2. There was no compensation for CPVC thermal expansion. 3. There was a general failure to meet the manufacturer's installation requirements. 4. Oxygen was allowed into a “closed” system. As a result, the air separator and pump impeller became corroded. 5. An unknown hydrocarbon contaminant was introduced that attacked the CPVC. Analysis The first set of photographs suggests a case where the threaded brass connections throughout the installation were improper for this application. NPT tapered threads (National Pipe Thread Standard) are designed to create interference fit between similar materials as a means of creating both a high-strength union and a positive fluid seal. Where one material is substantially stronger (brass) than its counterpart (CPVC), the strength of the union and the integrity of the seal may be compromised. Stress would be introduced that would accelerate the cracking and, ultimately, cause the failure of the CPVC.
Figure 1: Sample 3, CPVC thread vs brass nut tightened to .080 gap.
Figure 2: CPVC Thread effectively “bottomed out” on all samples. Note obvious leak path. In a proper application of CPVC threads, the manufacturer installation recommendation is to hand tighten for no more than one to two turns beyond finger tight, using a strap wrench. It is clear that these unions were tool-tightened to the point of CPVC material deformation, as the brass nut bottomed out on the CPVC male connector. This introduced mechanical stresses in the material. These stresses opened leak paths, while making the material more vulnerable to chemical contamination and degradation.
Figure 3: Severe galling of threads observed on all CPVC vs. brass samples
Figure 4: Evidence of leakage and corrosion of brass observed on all samples. Note tooling marks on CPVC connector.
Figure 5: Dark staining on threads and thread root is typical of contaminant absorption under material stress conditions.
Figure 6: Rust deposits, brass corrosion, evidence of leakage and Teflon tape remnants are consistent across all samples Classic environmental stress fracturing was found at the inside wall of the threaded area of the pipe. This is a precursor to failure because of excess mechanical forces applied to threads and the propensity for CPVC to absorb contaminants at such stress zones -- a textbook case.
Figure 7; Classic ESC. Brown stains are rust deposits remaining after gentle cleaning of the sample. This cross-threaded sample was found in the demolition pile for the concurrent re-pipe. This sample provides a particularly egregious demonstration of combined deficiencies observed in this CPVC installation. A catastrophic failure at this union was imminent.
Figure 8: Catastrophic failure was imminent CPVC is proven to be a robust piping material throughout the world, but when many adverse conditions are concurrent -- in this case, we had poor workmanship, multiple mechanical stresses, contamination and chemical attack -- no material is resilient enough to resist such abuse.
Figure 9: The anatomy of a failure
Figure 10: Radial and longitudinal ESC failures were present in the cross-threaded sample
Figure 11: Two complete cracks form inside the threaded section of sample 5. Note micro-cracking surface patterns.
Figure 12: “Dry desert” cracking pattern is typical of ESC.
Figure 13: This ECS failure attributed to poor workmanship as excess cement was allowed to pool inside the pipe. An additional sample provided by the heating contractor demonstrates a condition where insufficient cement was applied, allowing the CPVC tube to fall out of the connector. This is notable because the failed sample is not the original installation; rather, it appears to be a later repair. This would suggest that there might have been many hands contributing to the failure record of this facility.
Figure 14: An additional failure sample that was provided by the heating contractor does not appear to be an original installation. This suggests that even continued repairs would not necessarily guarantee a reliable system. Conclusion The architectural building specifications did not make it clear to engineering what material would be used for the piping of the hydronic system. The engineers designed a hydronic system without providing readily obvious identification of material. It appears from the drawings that a metal system was intended (given the omission of thermal expansion loops). In the absence of this specification, the builder or sub-contractor took it upon himself or herself to use an otherwise reliable industry standard such as CPVC piping product. Features such as thermal expansion loops and brass-inlaid connectors were not specified, so the contractor may not have known to include them. However, strict adherence to CPVC manufacturers installation requirements would have alerted the installer to seek additional information, if not to attend to industry practices. Further, the building was completed and operated without adequate regard for the make-up water pressure or constant venting for a closed system. A closed hydronic system would not hold enough oxygen to cause the iron corrosion that was observed. Only oxygen in the water would corrode the pump impeller. When the oxygen was inadvertently allowed to enter the system, that may have been when an incompatible corrosion inhibitor, cleaning agent or MIC inhibitor was also introduced. The incompatible chemical was likely absorbed in high-stress areas of the system such as the brass fittings and anywhere that unchecked thermal expansion would introduce stress. The system began to weaken. As repairs were made, they could not be attributed to any one cause because each occurred opportunistically at a microscopic level corresponding to invisible stress levels. Some failures were minor and some catastrophic. What is certain is that they would have continued until all components were replaced individually. Even then, those replaced components would have still been vulnerable to failure. A decision was made to replace a major part of the CPVC system with polypropylene. It was our recommendation to replace the entire CPVC system with an “engineered system” that is specified from beginning to end to perform the function of a modern and reliable hydronic heating and cooling system. Further, operating procedures and maintenance planning should be specified and overseen by a competent engineering firm that understands the vulnerabilities of all hydronic system components. Finally, if the owners want to determine exactly what chemical(s) was responsible for compromising the relative integrity of this CPVC system, further laboratory tests may be performed to extract the identity of the offending hydrocarbon. However, these are fairly expensive tests whose ultimate value ought to be weighed against the value of pursuing additional action. *** Dr. Duane Priddy, CEO of Plastics Failure Lab, whose assistance on this project is greatly appreciated, provided the following chart:
How to Prevent Failure in Water Systems
Engineers can help insurers spot pitfalls and mitigate the risks of CPVC systems before issuing a policy and inviting disaster.
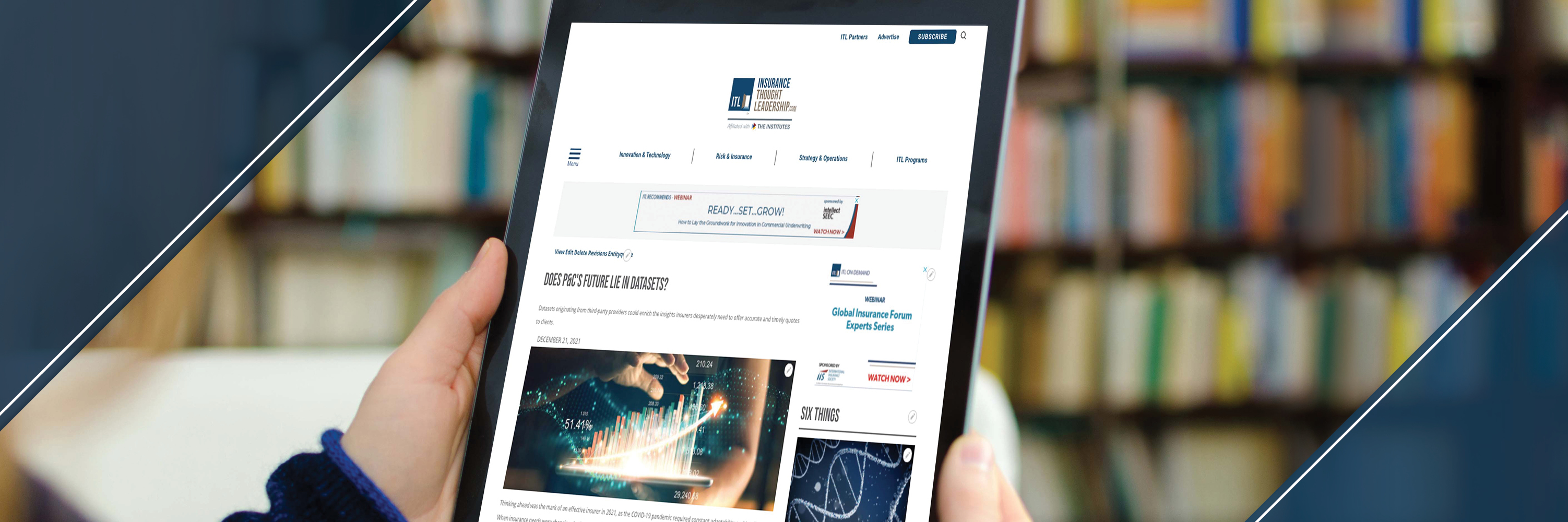